Robot Transfer Units
From packaging to automotive manufacturing, 7th axis robot transfer units (RTU) are picking up speed in many industries. These systems combine a linear actuator with a six-axis articulated arm or collaborative robot, creating a 7th axis of movement. This additional axis enables the robot to tend to multiple workstations or machines across a wider area of the factory floor, offering many advantages over stationary robotic setups.
The Many Benefits of RTUs
- High throughput. RTU systems eliminate the need to reposition multiple robots and workpieces, maximizing uptime. They can also transition quickly from one task to another simply by moving along the track, maintaining a steady work flow.
- Greater flexibility and safety. RTUs can accommodate floor, elevated and inverted mounting configurations, supporting more flexible factory layouts and enabling the system to be set up away from workers to boost safety.
- An ability to cover larger work areas. With the 7th axis, a robot can cover a lot of ground on the factory floor in order to perform multiple tasks.
- Better cost efficiency. By moving along a track to different workstations, a single robot can perform the work of many stationary robots without having to invest in additional costly robotic arm systems.
- Ease of integration. Many RTUs are compatible with a wide range of robot models, allowing manufacturers to upgrade their systems without an extensive overhaul of equipment.
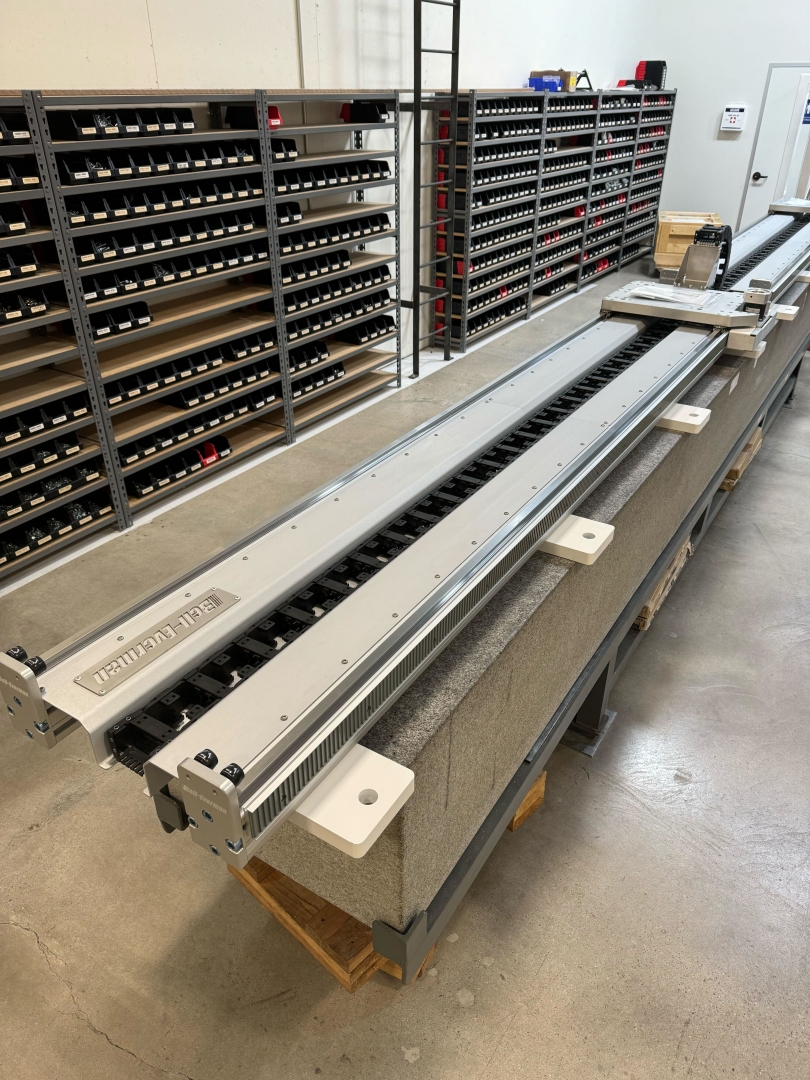
The Unique Advantages of ServoBelt™
The conventional design method for RTUs involves mounting the robot on a platform that runs along a linear track. You must also choose between a belt drive, which offers inexpensive but low fidelity motion for a single carriage, and a rack and pinion drive, which can handle higher payloads but is more costly.
Redefining this classic belt drive approach, our ServoBelt™ Linear Drive supports unique RTU capabilities — but without the cost and over-engineering pitfalls of traditional 7th-axis designs.
Multiple, independently controlled carriages on the same axis. A single ServoBelt™ Linear axis can support multiple, independently controlled carriages, enabling us to design RTU systems with multiple articulated robots and cobots running on the same motion axis.
Unlimited travel lengths. Due to a unique splicing method, ServoBelt™ Linear supports designs with unlimited travel lengths, enabling us to engineer very long RTU axes with multiple robots. This limitless scalability also avoids the performance and commissioning difficulties that can arise in long-travel applications with other motion technologies.
Avoiding the pitfalls of over-engineering. Our RTU systems are based on standard, off-the-shelf ServoBelt™ Linear building blocks, which enables us to minimize costs and meet aggressive lead times compared to traditional, over-engineered RTU systems.
Common RTU Applications
- Aerospace — composite layup and drilling.
- Automotive — drilling, welding, material handling and painting.
- Consumer goods — moving goods between different processing stations.
- Machine tools — moving castings or tending to injection molding machines.
- Logistics and packaging — palletizing, loading/unloading and transporting products.